We believe it’s safe to say that we all want our companies to be the best at what they do, make (and save) money, be as efficient as possible and grow. Preferably, all at the same time. 😉 In short: we want our companies to be healthy and reach their fullest potential. Yet… there are always challenges which slow us down and complicate the achievement of our goals. Various people want different things or maybe feel unappreciated, there is a lack of time and/or knowledge, people are afraid of changes and growth – which they see as a risk. All this results in missing great opportunities, wasting time and money, continuously putting out fires and being overtaken by events.Â
What if there is a possibility to reach the fullest potential as an engineering firm? What if we can offer you the right tools for:
… staying efficient while growing?
… exploiting the talents and expertise to the greatest possible extent?
… maintaining quality?
… saving time and money?
… keeping things fun and interesting?
… having the happiest (ch)employers and (ch)employees?
You are probably thinking ‘yes, that’s what I want, but wait… what is the catch?’ Well, honestly, we couldn’t come up with one. Of course, weigh things up properly and select what’s best for your company as there are always pros and cons in every way of working. How about this: we tell you about the tools and share the pros and cons for free, and you decide what your next step is going to be?
Traditional engineering organisations
Before we explain how to ‘do less and achieve more’ we need to take a step back. First, let’s take a look at a traditional engineering organisation. Many of these firms have line organisational structures with regulated procedures. Each organisation contains a division with its own responsibility. There is also a certain presence of hierarchy which causes impersonal relations. The result? Everybody does their thing and stays in their bubble without seeing the complete picture. And if there are any problems, most organisations are focused on treating the symptoms instead of attacking the root of the problem.
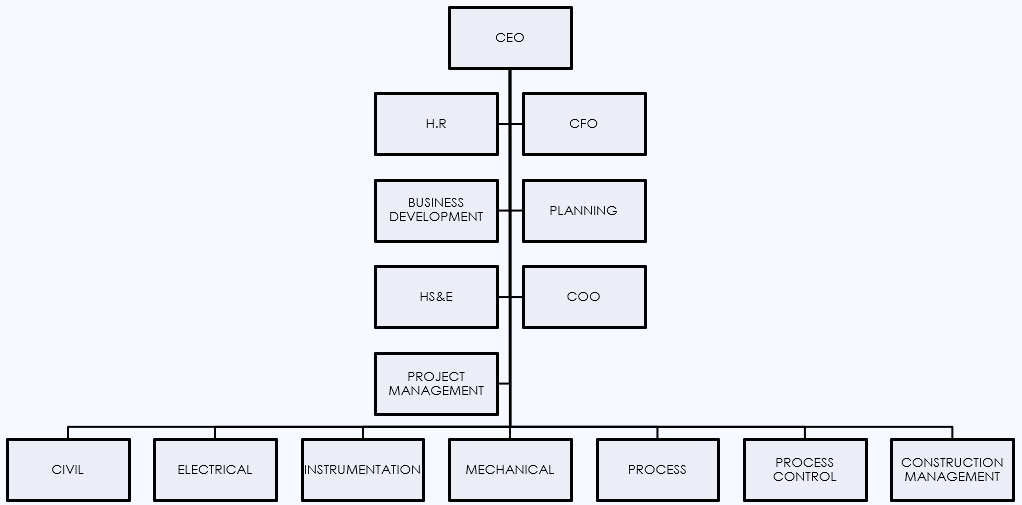
Traditional project flow
Each project usually has the same traditional project flow:
Stage 1: Planning and department leads look at the required hours.
Stage 2: Project has a kick-off with the project leads from all departments.
Stage 3: Project leads go back to their departments and divide the work.
Stage 4: Output created at one department will serve as input for another department.
Stage 5: Project deliverables are handed to the client.
What usually happens…
– Because of tight schedules and deadlines, some departments work while lacking the input from other departments.
– There are miscommunications between departments because input documents used in their work suddenly change. Which, of course, weren’t even finished in the first place.
– Calculated engineering hours already spent with the wrong input.
– Panic. Needless to explain how people react in panic situations.
– Departments start blaming each other.
– More engineers are put on the project to make the deadline.
– Project is finished with a loss.
The unnecessary consequences…
– Department leads estimate more hours in following projects to cover for these inefficiencies.
– Engineers have way too much time to do their work at the start of the project due to this overestimating.
– At the end of the project, the engineers are lacking time to re-do their work.
How to do things differently and avoid unnecessary, time-consuming problems?
It is proven that flat hierarchies are necessary for companies to be successful. They encourage (ch)employees to use their creativity to solve problems and provide brilliant solutions. (Ch)employers who give their (ch)employees the freedom to make their own decisions and being creative, will get more engaged, productive and happy (ch)employees in return.
The rules of the game:
– Lose departments and create ‘project teams.’Â
– Each team requires all competencies as this way everybody can learn from each other and add their value.
– Eliminate middle-management.
– Project teams handle their own (project) management.
– Everyone helps each other during the project (“cross-departmental”). Depending on the phase of the project, this could mean the process engineer would assist the instrumentation engineer with small tasks.
– No official seniority among team members (of course there will be natural seniority).
– Project teams are coached (not managed!) by experienced engineers with strong interpersonal skills.
– If specific knowledge is required, it can be found in other teams or externally.
– Staff functions are supporting, not leading.
An improved engineering organisation
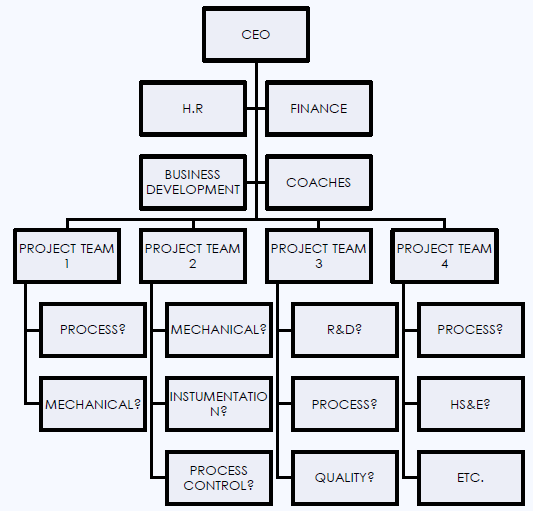
Advantages
– Small group working together creates harmony and fewer miscommunications.
– Knowledge sharing between engineers with different specialities.
– From the beginning, the right start since the input is clear within the project team.
– Team members feel they have responsibilities.
– Less overhead.
Disadvantages
– This way of working may look less efficient at first. This is because the specialistic work will be done by engineers who are not familiar with particular work. However, this can be easily solved as every speciality is available within reach.
– There will be no clear leader or project manager who will make the final decision. In our experience, most people can achieve great things, if you give them the freedom to be themselves and excel in what they do. 😊
So, do you want your organisation to be healthy and reach its fullest potential? What are you waiting for? We are glad to help you, because if you’re happy; we’re happy. As cheesy as that may sound. 😉
Are you looking for a career in chemicals, food, or life sciences? Check Our Work. Can’t find the right vacancy? Let us know! We have more to offer. 🙂 Follow our LinkedIn company page!Â